Uzina de Vehicule Dacia, situată pe platforma de la Mioveni, Argeș, se pregătește să intre într-o nouă fază de transformare, pentru a găzdui producția a două modele importante pentru marcă. Primul va fi Duster 3, o nouă generație care va începe să fie produs în acest an și va ajunge la clienți la începutul anului viitor. Al doilea va fi Bigster, cel mai mare automobil produs de Dacia vreodată.
O mașină la fiecare 55 de secunde, acesta este ritmul actual al uzinei Dacia din România. Fabrica în care sunt produse două dintre cele mai vândute mașini ale Europei, Sandero și Duster, a reușit să revină aproape de capacitatea maximă de producție, după perioada lungă în care s-a confruntat cu penuria de componente electronice, dar și cu probleme de logistică la nivel internațional. Acest lucru a adus o scurtare a timpului de așteptare pentru clienți, însă, în continuare, pentru o mașină comandată se poate aștepta între o lună și trei luni.
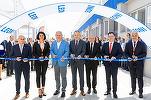
3 aprilie - Eveniment Profit Health.forum - Sănătate nouă
16 aprilie - Maratonul de Educație Financiară
Pentru a începe producția noilor Duster și Bigster, Automobile Dacia va fi nevoită să pregătească tehnologiile și utilajele specifice, activitate care se va desfășura în lunile următoare. Până atunci, activitatea continuă pentru a satisface comenzile de automobile din Europa, adunate în ultimul an, pe fondul crizei de semiconductori.
Uzina de Vehicule Dacia: 65% din producție sunt mașini Duster
Unul dintre cele mai importante departamente în Uzina de Vehicule Dacia este Presajul, unde cele 900 de tone de tablă procesate zilnic se transformă în componente de caroserie. În zona numită High-Speed, care a fost dezvoltată, în perioada aprilie 2018 – iulie 2020, cu o investiție de 37 de milioane de euro, sunt produse panourile de uși, capota față, pavilionul mașinilor, adică cele mai vizibile componente ale unei mașini.
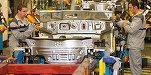
Linia este una de mare viteză, așa cum îi spune numele, având o capacitate de 18 curse pe minut, și permite realizarea până la 3 piese într-o singură cursă. Cei de la uzină spun că linia de mare viteză poate realiaz până la 9.600 de piese pe schimb. Și timpul de schimbare a matrițelor pentru piese este mult mai scurt, 3 minute, față de cele 40 de minute necesare unei linii TGP, lente. Aici au fost produse primele piese pentru noua generație Sandero, dar și pentru Duster, începând din iulie 2020.
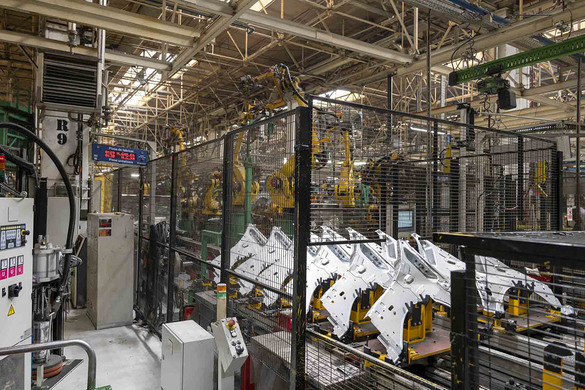
Linia de mare viteză cuprinde 4 prese ROTEM, fabricate în Coreea de Sud, 5 roboți inter-prese, furnizați de compania GUDEL, din Elveția, și 4 roboți FANUC pentru începutul și finalul liniei (fabricați de compania Daebong din Coreea de Sud). Pe aceste utilaje sunt produse 32 de game de piese ambutisate pentru toate vehiculele Dacia.
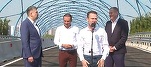
După Presaj, procesul de producție merge în Departamentul Caroserie, care se întinde pe o suprafață de 6,5 hectare, în care lucrează 1.780 de angajați, în ateliere de fabricație, de mentenanță, proiecte noi și piese de schimb și CKD. Departamentul are două fluxuri de asamblare, din care unul dedicat Duster, unde sunt produse 40 de vehicule pe oră, și unul dedicat celorlalte modele, Jogger, Logan, Sandero Stepway și Duster, cu 35 de vehicule pe oră.
Aici „muncesc” 556 de roboți Fabuc și ABB, care au făcut ca procentul de robotizare să ajungă la 44%, procent care va urca la 52% odată cu startul noului Duster.
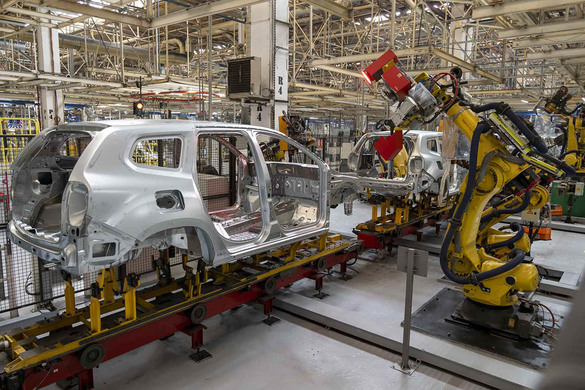
Mai departe ajungem la Montaj Vehicule, departamentul în care piesele încep să fie puse cap la cap pentru a se transforma într-un automobil. Pe 6 hectare, cei 1.713 angajați sunt distribuiți în mai multe ateliere, la fel ca la Caroserie. Ritmul de asamblare urcă într-o zi plină până la 1.392 de mașini, adică 65 de vehicule pe oră sau o mașină la fiecare 55 de secunde. Linia de asamblare se întinde pe o lungime de 1,2 kilometri și găzduiește de la primul post de lucru și până la ultimul 172 de vehicule.
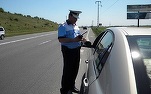
În acest moment, mixul de producție acoperă 65% mașini Duster, 25% Jogger și 10% Sandero Stepway și Logan. Fluxul pe linii include montajul pe caroserii pentru fiecare dintre componentele cunoscute, de la motor și axe, până la tapițerii și detalii estetice.
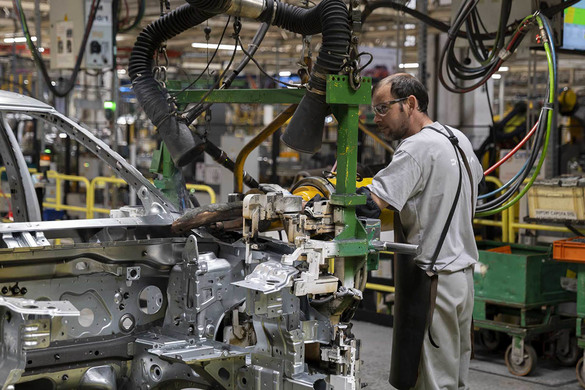
Odată finalizat fiecare vehicul, dar și pe parcursul asamblării, intră în funcțiune Departamentul Control Calitate Montaj Vehicul, care este format din personal în posturi de control, control vehicul finit și plan de supraveghere frecvențial și evaluare produs finit. Departamentul are 243 de responsabili de calitate, care sunt prezenți în toate departamentele de fabricație, dintre aceștia 33% fiind femei. Nu mai puțin de 80% din personalul de control își face treaba direct pe fluxul de fabricație, iar 15% fac activități de supraveghere frecvențială. Sunt 800 puncte de control pe cele patru tipuri de caroserii, cu o paletă diversă de motorizări, cutii de viteze și versiuni de echipare.
Există așa-numita cameră calmă, în care vehiculele sunt verificate timp de 15 minute, de către 9 operatori, pe două linii. Mașinile sunt verificate funcțional, la nivelul aspectului exterior și interior, precum și la cel al funcționalității multimedia. Vehiculele sunt validate și puse în parametri pe standuri de reglaj și control, la direcție, sistem de faruri, asistență (ADAS). Pe bancurile de validare electrică și electronică se va și primele rulaje care simulează utilizarea de către client.
Uzina Mecanică, cea mai mare turnătorie din Group Renault
Separat de Uzina de Vehicule, Uzina Mecanică și Șasiuri, care urmează să fie separată pentru crearea viitoarei divizii Horse, este cea care produce motoarele și cutiile de viteze, fiind una dintre cele mai complexe uzine de acest tip din Renault Group. Aici se fac activități de turnare, uzinaj, asamblaj, presaj, sudură și cataforeză, proceduri complicate care țin în mare de metalurgie.
Aici sunt fabricate diferite componente de aluminiu, motoare cu combustie, cutii de viteze, precum și elemente de șasiu care merg mai departe atât în Uzina de Vehicule, cât și în alte uzine ale Renault sau ale Alianței Renault – Nissan – Mitsubishi. La Mioveni este și cea mai mare turnătorie de aluminiu din Renault Group, în care sunt turnate 29.000 de tone de piese pe an.
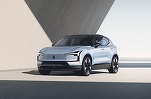
Uzina Mecanică produce motorul HR10, pe benzină și GPL, TCe 90 și, respectiv, ECO-G 100, care este instalat pe toată gama Dacia (mai puțin Jogger) și pe modelul Renault Clio. De asemenea, produce cutiile de viteze manuale, cu 6 trepte, având două versiuni, una pentru modelele cu tracțiune față, alta pentru Duster 4x4, pentru care produce și modulul de transfer punte față și cel pentru puntea spate.
Componentele pentru tracțiunea 4x4 sunt exportate în toate uzinele în care se asamblează Duster cu tracțiune integrală, sub marca Renault. Uzina Mecanică produce o parte din componentele integrate în motorul HR10, începând cu carterul, semela, carterul distribuție, în timp ce chiulasa, volantul, arborele cotit, arborii cu came și bielele sunt aduse de la furnizori.
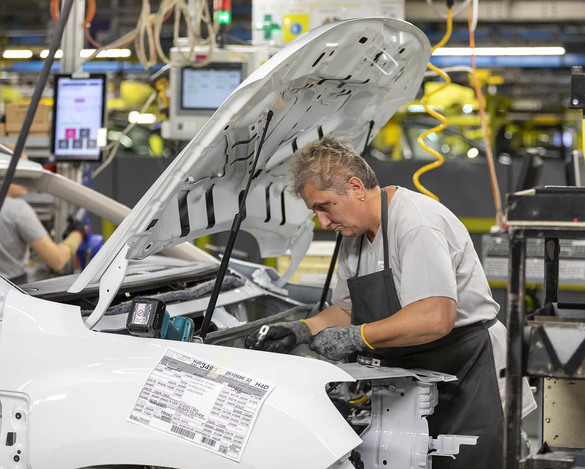
Pentru carter, se realizează o operațiune în premieră, cu tehnologia BSC, care permite pulverizarea de cămăși pe cilindri dintr-un strat de aliaj de oțel. Noua tehnologie contribuie la reducerea frecărilor din cilindru.
Capacitatea de asamblare a liniei de motoare este de până la 526.000 de motoare pe an. Linia este automatizată la nivelul transportului de piese, cu sisteme AGV (Automated Guided Vehicles).
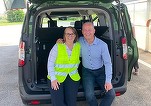
Controlul de calitate la motoare se face prin testări pe stand, atât la rece, cât și la cald, fiind urmăriți 150 de indicatori de calitate și performanță. Controlul se face și pe linie, de către operatori, cu diferite dispozitive digitale prin care pot semnala probleme de securitate și calitate.
Activitatea de producție de motoare și cutii de viteze va fi integrată în viitoarea companie Horse (numele real încă nu este anunțat), care va cuprinde toate uzinele de motoare din cadrul Renault Group, în asociere cu uzinele de motoare ale Geely.
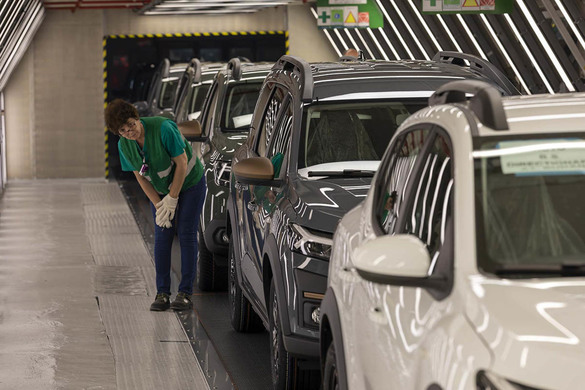
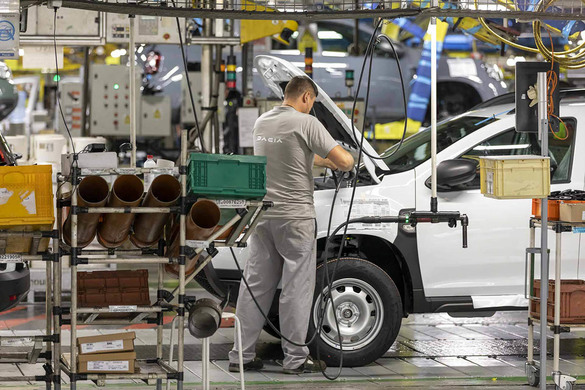
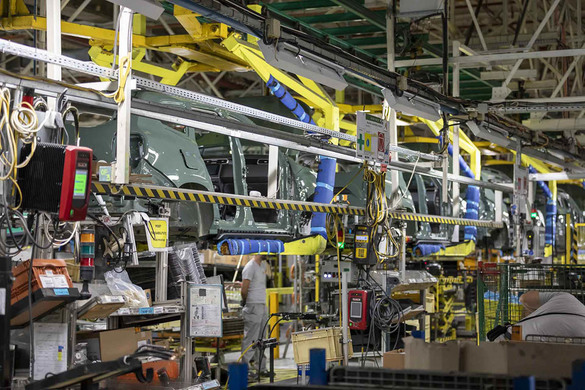
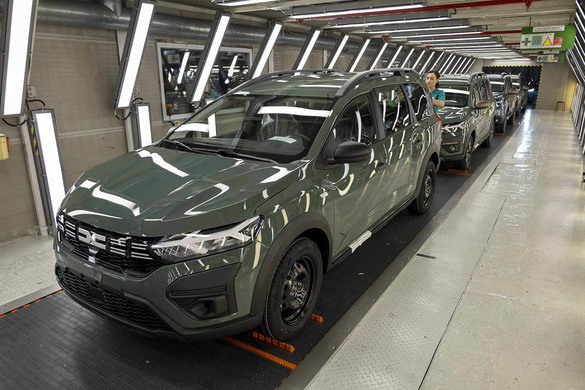
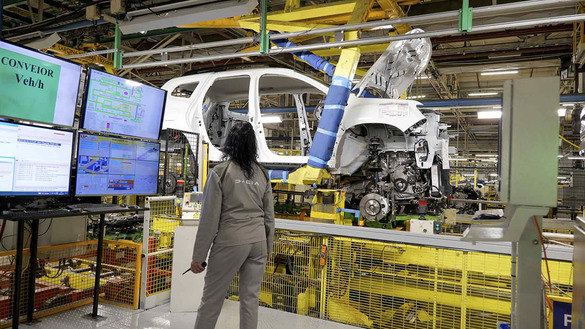
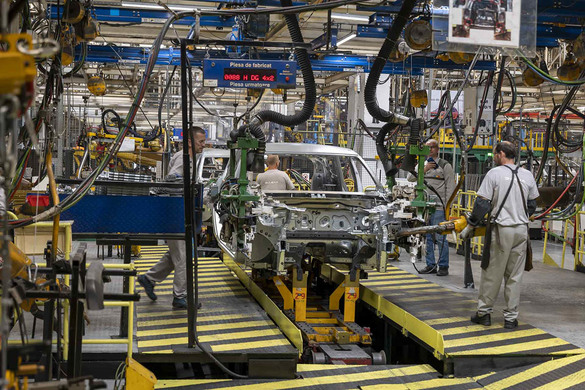
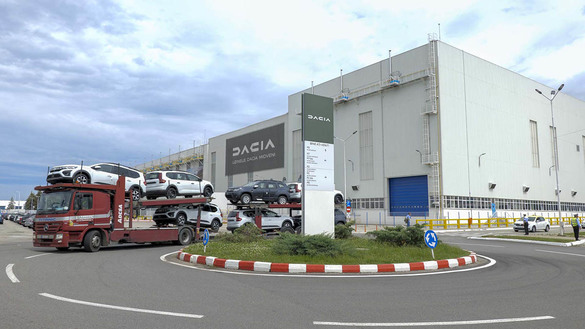